The crude tin electrolysis method is a widely used pure tin process. It is a process that converts crude tin liquid containing impurities into high-purity tin through electrolytic equipment to meet various industrial and military needs.
The characteristics of the crude tin electrolytic purification process are: ① shortened operation process; ② high useful metal content, ③ high tin yield, easy mechanized production and other advantages.
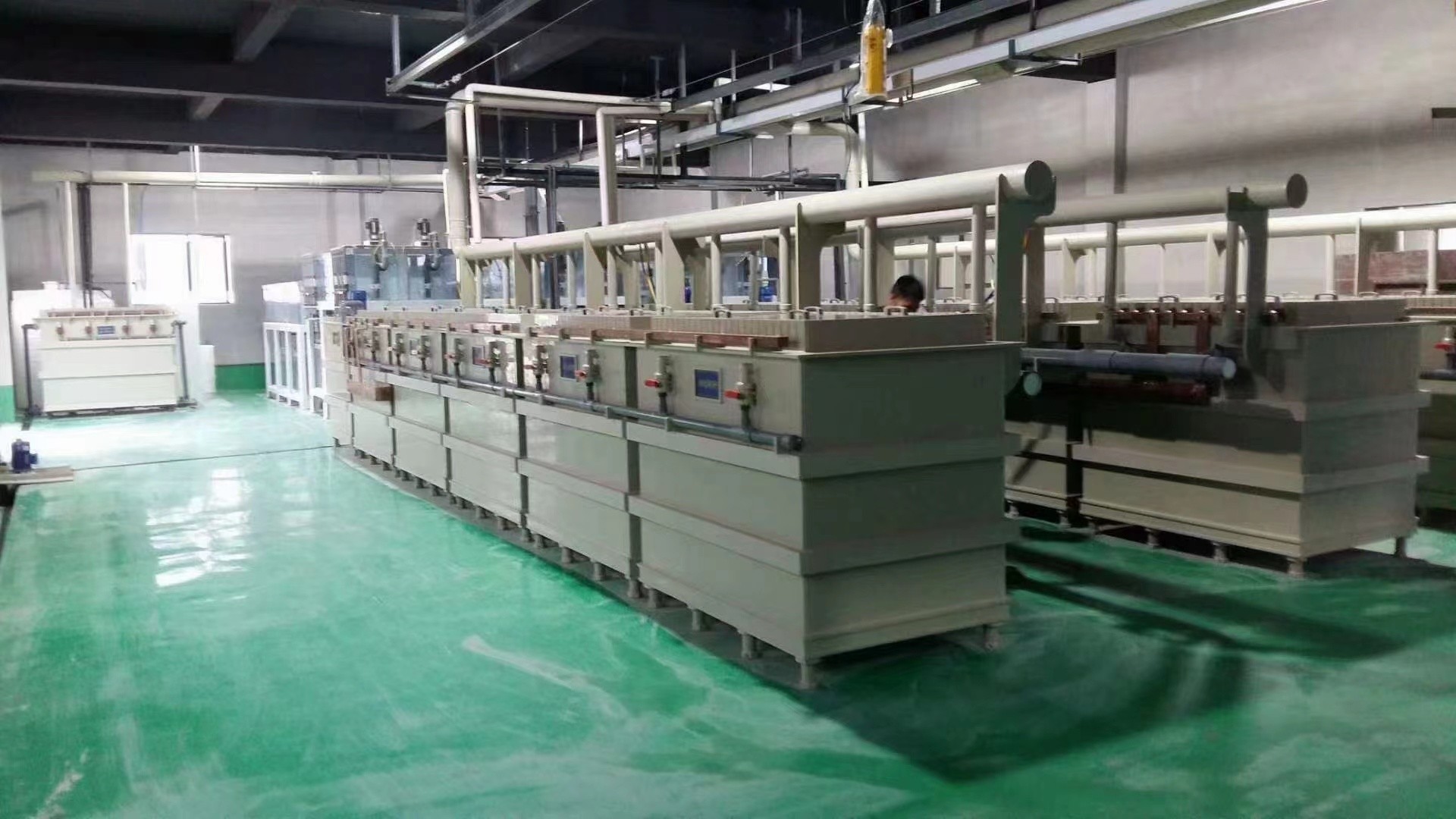
The electrolytic production process of crude tin includes charge preparation, reduction smelting, tin discharge, slag discharge and other processes.
Charge preparation
In the process of electric furnace smelting, the calculation of raw material ratio is roughly the same as that of reverberatory furnace tin smelting. The charge can be powder ore, granular material or block material, which is sent to the top hopper of the furnace by stirring and then added in batches. When charging for the first time, the moisture content should be controlled below 2%.
Reduction smelting
Batch feeding is adopted, and the first batch of materials accounts for about 1/3 of the total amount. At the beginning of smelting, the current is controlled at a small value. After a certain amount of slag and crude tin is produced, the current is increased and the second batch of materials is added at the same time. After that, a batch of materials will be added every 2 hours, and all the materials will be added within 10 to 12 hours. The reduction and slag-making process of electric furnace smelting occurs almost simultaneously with the heating of the furnace charge, and the melt relies on the convection circulation of the superheated slag near the electrode to transfer electricity, heat and mass. The crude tin and slag produced are clarified and layered in the furnace.
The batch feeding method is adopted, and the first feeding is about one-third of the total feeding material. In the early stage of smelting, the current is first adjusted to a low level. After a certain amount of slag and crude tin are generated, the current is increased and the second charge is added. After that, a batch of materials will be added every 2 hours, and all the materials will be added within 10 to 12 hours. In electric furnace smelting, the reduction and slag-making process is carried out simultaneously with the heating of the furnace charge, and the melt mainly relies on the convection circulation near the superheated slag to transfer electricity, heat and mass. The crude tin slag produced is layered in the furnace.
Slag and tin discharge
The process of multiple tin discharge and one slag discharge is adopted. After half of the material is fed, the first tin discharge begins, and each furnace is discharged 3 to 4 times. After the last batch of materials is added and melted, add the last tin, and then release the slag once. The crude tin contains 97% to 98% tin. After the slag is released, it is concentrated in an electric furnace for the second smelting, or it can be carried out without releasing the slag.
The electrolytic refining technology of crude tin has become one of the mainstream processes in the tin processing industry, with the advantages of high production efficiency and high product purity.
A new technology of multiple tin release and one slag release is proposed. When the material is half full, the first batch of tin is added, and one furnace is added 3-4 times. After the last addition and melting, the last tin is added, and the slag is thrown out once. The content of crude tin is between 97% and 98%. After the slag is discharged, it is concentrated in an electric furnace for secondary smelting, or it is not released and the secondary smelting is continued.
The purification of crude tin electrolytic equipment is an efficient and high-purity tin smelting facility.