Copper and its copper alloys are widely used in power, electrical engineering, thermal engineering, chemical engineering, instrumentation, shipbuilding and machinery manufacturing due to their excellent electrical and thermal conductivity, corrosion resistance, wear resistance and excellent plasticity. However, the resources are scarce and the price is expensive. Therefore, using copper anode furnace for fire refining is of great significance for saving copper resources and reducing production costs.
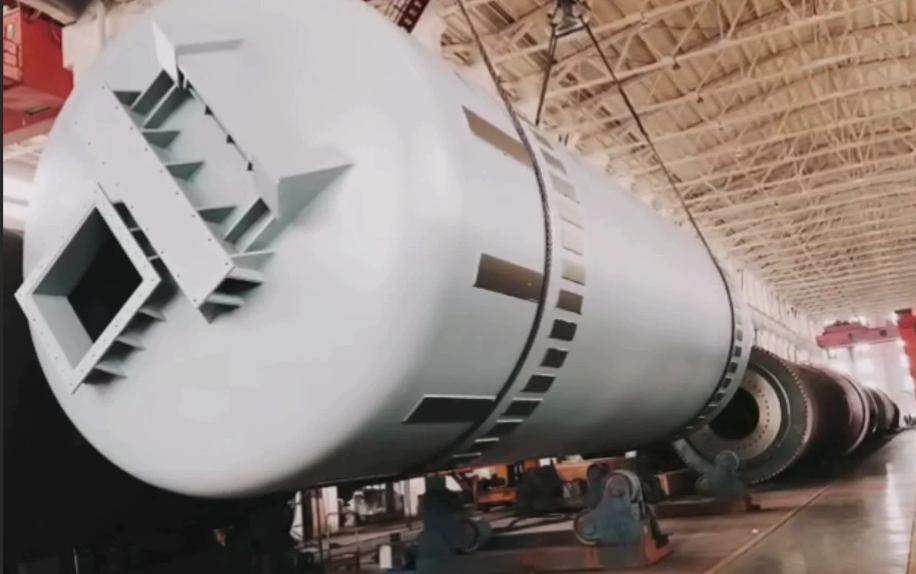
As mentioned above, fire refining is mainly divided into oxidation stage and reduction stage. Impurities in copper liquid are oxidized and removed at a high temperature of 1200°. After this stage, the copper solution will contain a certain amount of oxygen, which needs to be reduced to remove oxygen. In this stage, coal powder is used as a reducing agent. After all the steps are completed, the copper is cast to obtain anode copper with deoxidation and impurities removed. In this process, it should be noted that the slag is not allowed to contain magnesium bricks, graphite rods, oxygen tubes, bricks and other debris. The raw materials must be strictly inspected before entering the furnace. Iron parts, iron filings, bricks, stones and other debris are not allowed to be mixed into the purple copper, and yellow copper and untriggered shells, closures and other flammable items are not allowed to be mixed. After sorting the loose materials, they are bagged. Large and overlong pieces must be dismantled and bundled. The weight of the bags and bundles shall not exceed 50kg.
The fluxes for refining furnaces include quartz, coke, and lime, which all have certain technical standards. The quartz particle size is preferably controlled at 3-15mm, and no foreign inclusions can be mixed in. The coke particle size is less than 40mm, and the calcium oxide content in the lime is greater than 80, which is suitable for making alkaline slag in the refining furnace. In addition, attention should be paid to the preparations for the copper anode furnace before baking.